Prototyping
Accelerate Product Development and Design, Quickly & Affordably
Redefine Your Part Design Process with Precision and Reliability
Rapid Product Development and Manufacturing
At Blue Collar Engineering, we're dedicated to taking your vision from concept to mass production, or anywhere in between. Our Prototyping services exemplifies our commitment to excellence through rapid 3D printing services, guided by seasoned engineers adept in DFM (Design for Manufacturing) principles. This process of optimizing a design allows for ease of manufacturing and assembly with the goal of decreasing production time and lowering your cost.
.png)
How Prototyping Works
The prototyping stage can be a simple proof of concept or a systematic process of developing a product to test its feasibility, functionality, and design before full-scale production or implementation. This iterative process typically involves the following steps:
-
Identify Requirements: Understand user needs and objectives
-
Conceptualization: Generate ideas and visualize solutions.
-
Design: Develop detailed prototypes using specialized software.
-
Prototype Development: Build physical or digital prototypes.
-
Testing and Evaluation: Assess performance, usability, and suitability.
-
Iteration: Refine based on feedback and insights.
-
Validation: Confirm prototype meets initial goals.
-
Finalization: Prepare for production or implementation.
Prototyping is often a hands-on process. Our in-house capabilities and experience is what sets Blue Collar apart as the local leader in prototyping services.
Benefits of Prototyping
-
Cost-effective proof of concept.
-
Allows the customer to hone in on the final design for a fully functional, market ready product.
-
Helps you prepare for manufacturing by incorporating DFM (Design for Manufacturing).
-
Design flaws, improvements, and other modifications are brought to light and can be addressed early to maximize cost efficiency.
Cost Efficient In-House Prototyping
Blue Collar’s engineers and designers are hands-on during the building stages of our prototyping projects, which increases quality and gives us a better understanding of our customer's point of view. The many lessons learned during these builds are invaluable, as we are able to apply this knowledge towards future and ongoing iterations. Ultimately, this commitment to excellence ensures that our customers receive nothing but the best-in-class products.
In-House Machining and Fabrication
The capability to conduct in-house machining and fabrication can significantly accelerate the prototyping timeline while also maintaining cost efficiency. With expedited turnaround times, our in-house prototyping services provide our clients with a competitive advantage, particularly in fast-paced market environments where timing is critical.
Leveraging our expertise in both large-scale and small-scale manufacturing, alongside our patent knowledge, we offer comprehensive guidance throughout the entire prototyping journey.
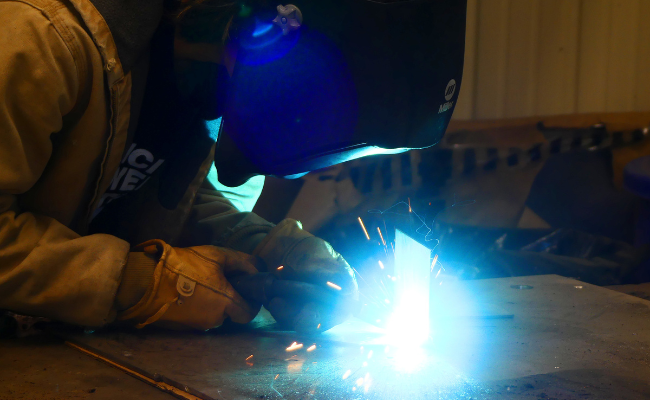
.png?width=650&height=400&name=Prototyping%20Slider%202%20(1).png)
%20(1).png?width=650&height=400&name=Prototyping%20%20CNC%20Machining%20%20(4)%20(1).png)
.png?width=650&height=400&name=Prototyping%20Slider%203%20(1).png)
3D Printing
3D printing has huge benefits in prototyping because of how cost effective it is as well as how quickly it can be done. Hundreds of different materials can be tested to determine which one performs the best. You can get results similar to injection molding, but without the price tag of injection molding.
We have access to several different technologies that can be used with prototyping. These include:
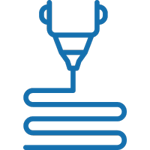
Blue Collar offers in-house FDM printing to bring computer models to real life parts for testing and analyzing.
This additive manufacturing technology is best suited for rapid prototyping and proof of concept. It is known for speed, low cost, and building volume.
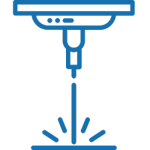
SLS produces parts that behave similar to injection molded parts and are capable of holding much tighter tolerances than FDM. Additives can be utilized as well to strengthen the parts if necessary.
This additive manufacturing technology is best suited for highly accurate and durable parts and is a proven method for saving both time and money.
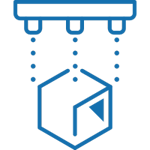
This cutting-edge additive technology is perfect for creating vibrant and intricately designed demonstration models in a fraction of the time.
With its ability to capture fine surface details and deliver a flawless finish, this method is the go-to choice for producing visually stunning prototypes.
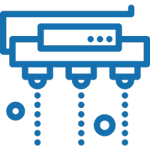
MJF technology is known for its ability to create intricate parts with precise details and consistent mechanical properties in a fast manner.
This versatility makes it a sought-after choice for a range of applications, from developing functional prototypes and bridging production gaps to efficiently producing low to medium-volume parts.
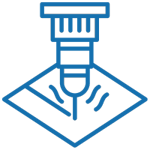
With this cutting-edge metal additive technology, you can swiftly create and refine prototype part designs without the need for costly tooling.
Plus, unlike alternative metal additive methods, DMLS parts skip the extra sintering step, resulting in quicker production times.
Interested in more Prototyping information?
Get in touch. Request a quote and get more information on all of your project's needs.